DESIGN
Gusberti Marcello’s design process is performed with traditional methods by a team of skilled engineers with many years of experience in valves environment. Design is strictly based on compliance to standards. During the past years, know is accurately maintained, structured and enriched by production feed-back. In fact one of key point of Gusberti Marcello’s design department is the strong interaction with production department, as the “PROGRAM manager” has responsibility of the whole result during all over the process, included the production process till the final control. Design characteristics are settled up to suit the working conditions, provide a high safety factor and prolonged, efficient service, as old customers can appreciate.
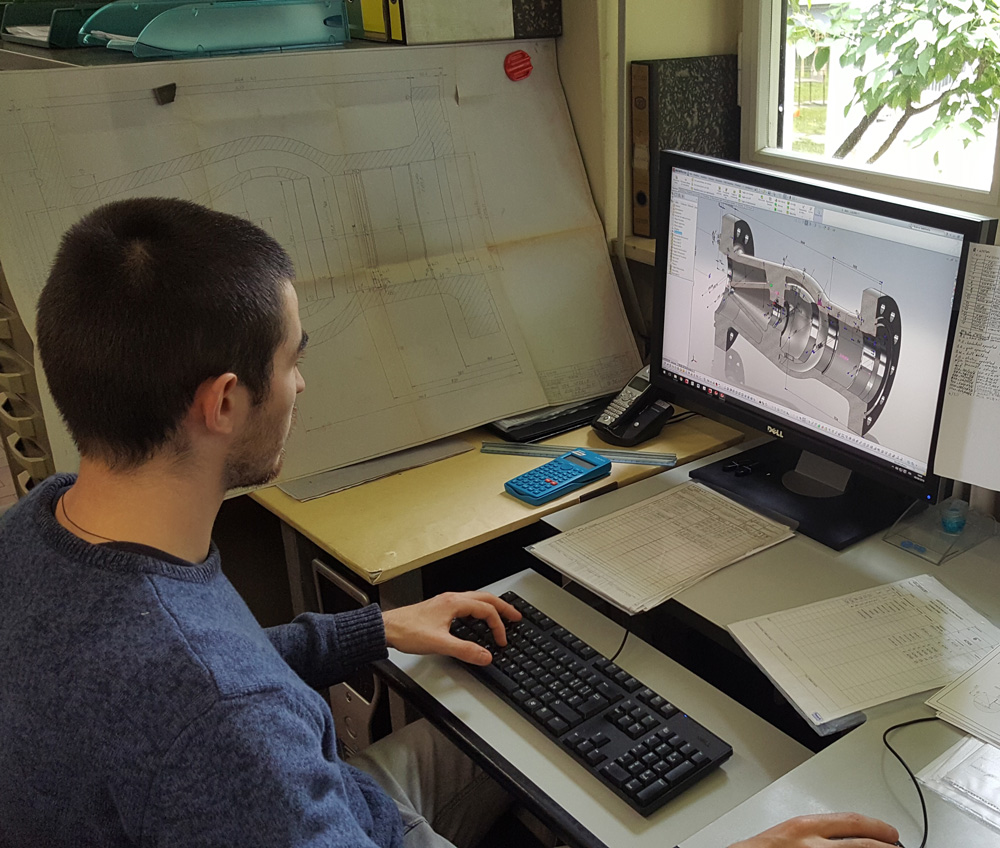
PATTERN FITTING
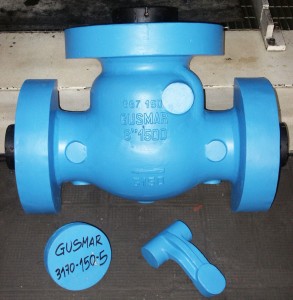
Gusberti Marcello assigns to this activity strong attention, as it is considered the base of a good result of the valve casting. Construction of patterns is in accordance with the most up-to-date requirements of good practice of casting. In fitting an old or in building a new pattern, this preliminary activity is realized by Gusberti itself or by specialized suppliers. The company has a stock of hundreds of models of valves.
SUPPLY AND JOB MANAGEMENT
The supply process (materials and equipment) is set by the “JOB manager”. Gusberti Marcello’s suppliers panel is composed by Italian suppliers for most part of components. Most critical supply are casting and steel bars. As casting suppliers Gusberti Marcello buys from Italian and European foundries with accreditation ISO 9001 and with big experience in the area of valves casting, each one specialized in particular kind of steel. All the casting houses are provided by a test laboratory to carry out the whole panel of tests requested by the 3.1 certification according to UNI EN 10204, and more (ex. radiographic controls). Inspection of rough casting are carried out to ensure soundness and uniformity. The compliance of materials to the orders are strictly checked, physically and chemically. Relating to steel bars Gusberti Marcello buys from biggest producers selected for type of steels; all the materials bought are provided by a 3.1 certificate according to UNI EN 10204.
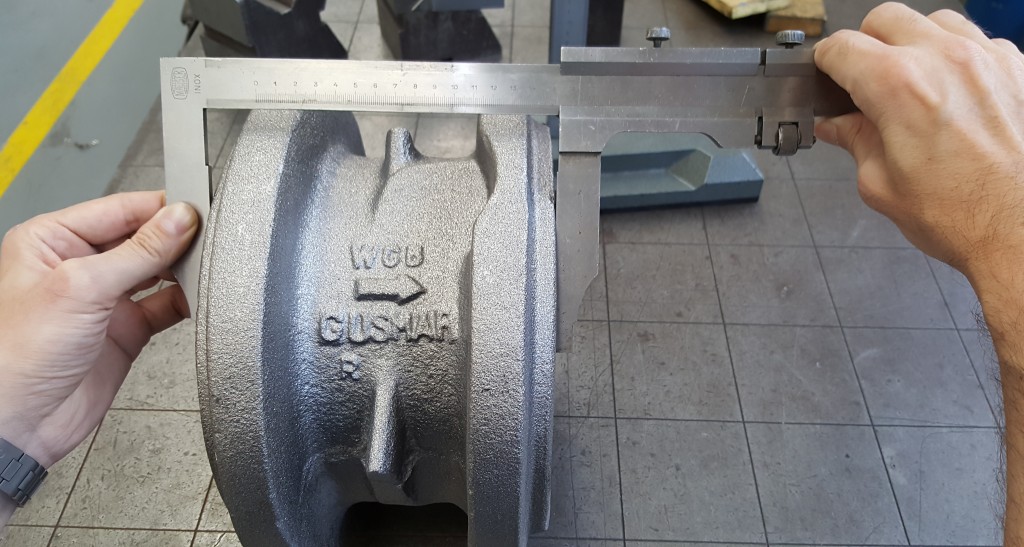
PRODUCTION PROCESS
IN-COMING CONTROLS
Our suppliers are historically tested and developed, but anyway Gusberti Marcello performs in-coming controls on every product to check the compliance of the supply to the order.
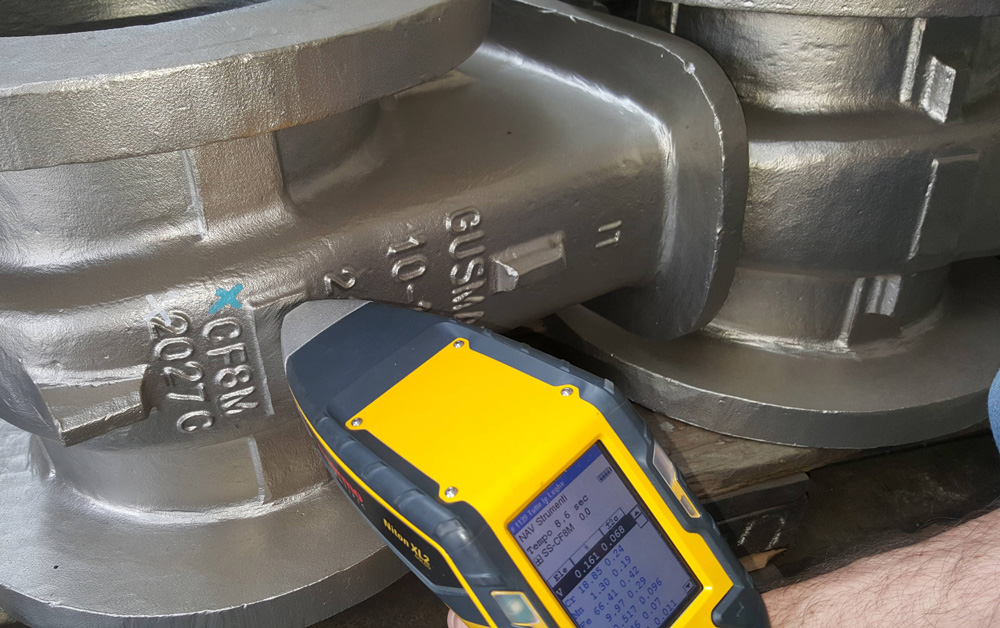
COMPONENTS MACHINING
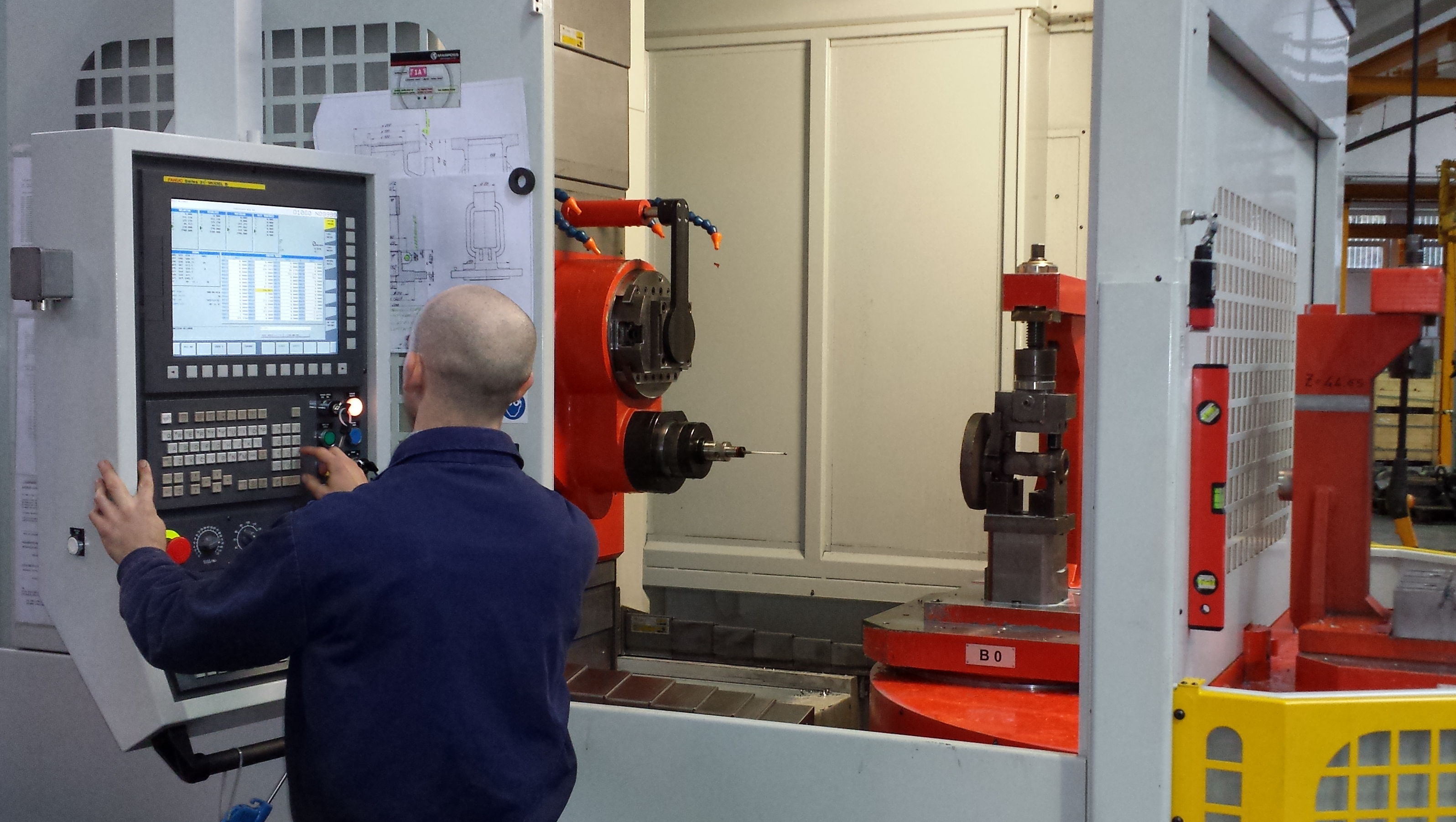
Casting and bars for critical components are completely worked inside the plant. Working components are run out on tooling machine both traditional then CNC. The company plant has got about 30 machines everyone of high reliability, included ADVANCED MACHINING CENTERS suitable for working of big body valves till DN 1400, working on 6 axes, which have very high performance on precision, timetable production and on set up flexibility. Overlay process, where necessary, are carried out by operator qualified by ASME section IX, both on automatic and manual welding machine.
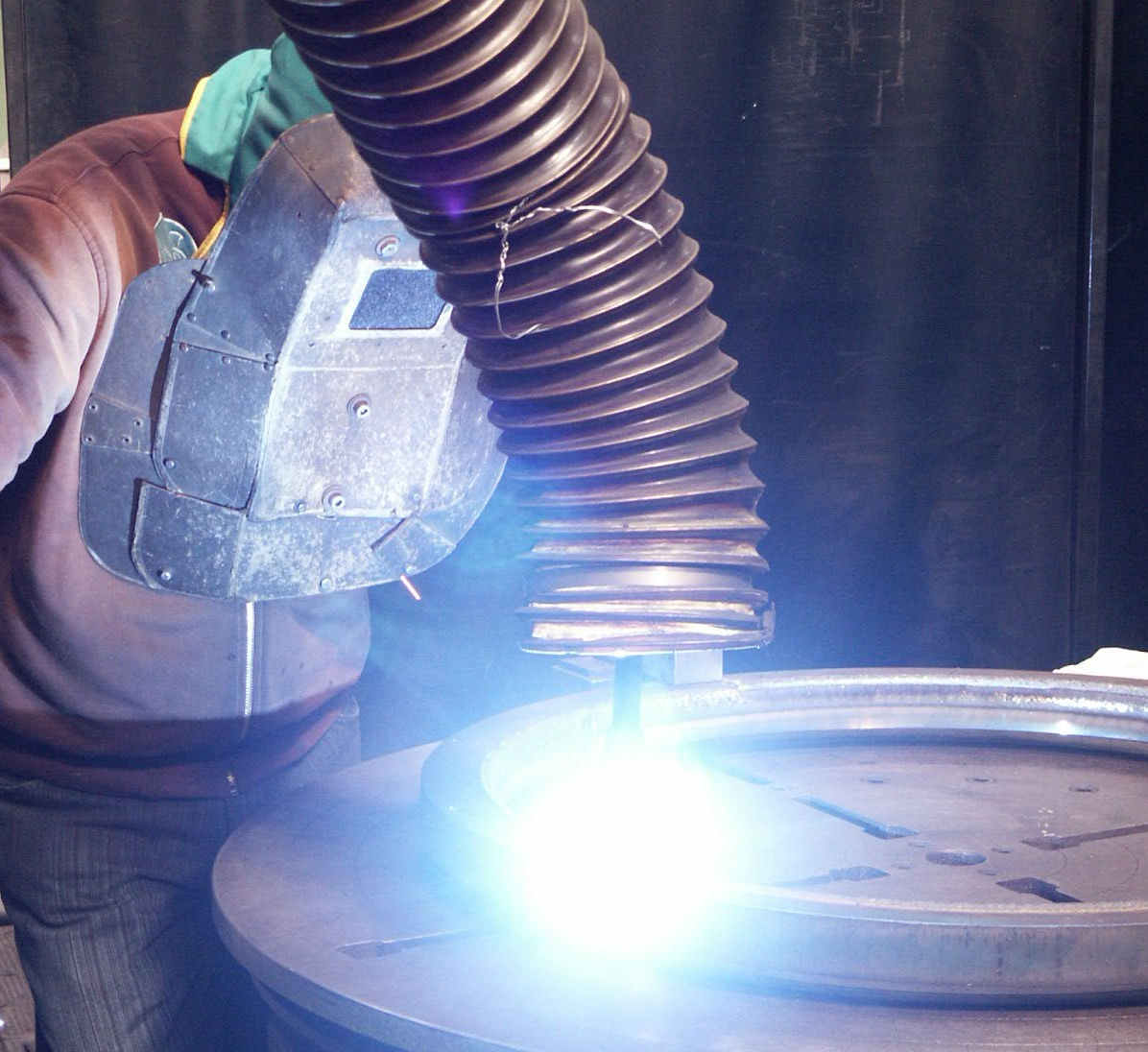
PRODUCTION CONTROLS
On all over the previous stages, production department conduces rigid inspections of dimensions, finishing, fitting of the valve parts, welding process results with the production responsible supervision. Where required casting can be subjected to Non-Destructive Test, including Magnetic particle, liquid penetrant and radiographic examination. The gauge employed for measurement and test are manometers, thickness meter UT, durometer, micrometers for internal and external, comparators, sliding gauges, everyone periodically verified by calibration procedure.
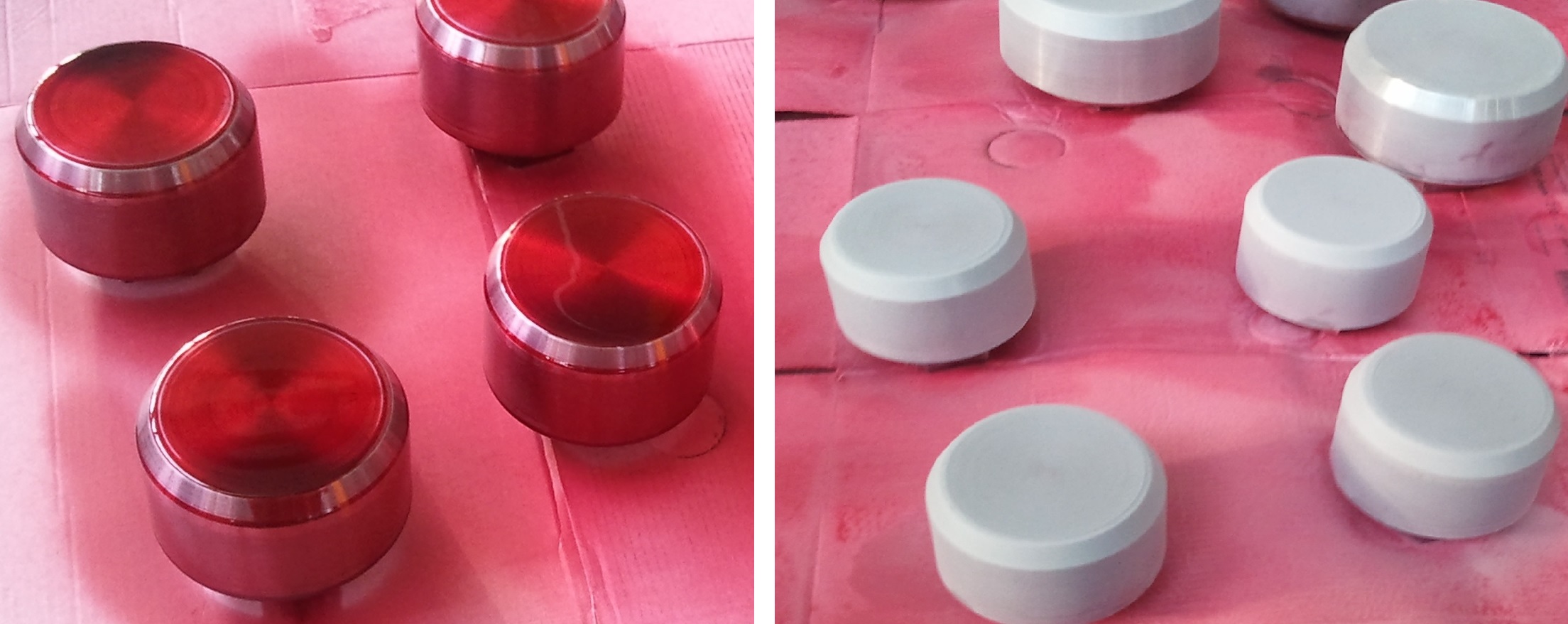
PRE-ASSEMBLY AND ASSEMBLY
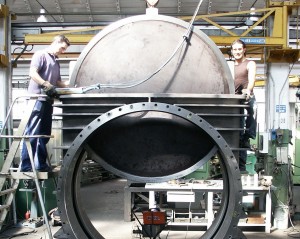
In the different steps of production working components are controlled to obtain a correct coupling between the parts as critical components are co-worked a pre-assembled. Final assembly are carried out by experienced operators.
FINAL INSPECTION
Final inspections are conducted by qualified operators on 100% of valves before painting (there necessary) and includes dimensional, visual, but especially strict hydraulic pressure tests of all seating surfaces, according to prescriptions and acceptance criteria of required specification. Hydraulic tests are performed on specific test machines that allows to test the seal, and the body of the valve. All the instruments for the tests are periodically controlled by the specific calibration procedure.
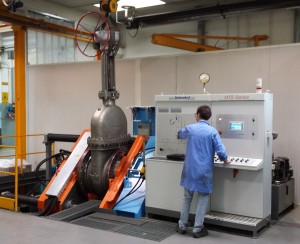
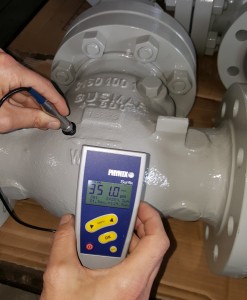